CIC nanoGUNE and CIKAUTXO join forces to optimize rubber
CIC nanoGUNE, the Nanoscience Cooperative Research Center, and CIKATEK, the R&D&i unit of CIKAUTXO, are working together to obtain rubber with high added-value by applying nanotechnology.
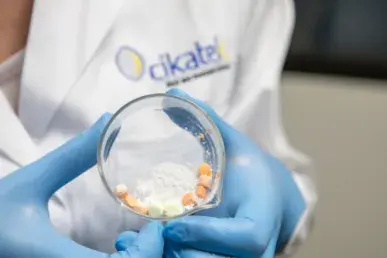
Rubber is a type of elastomer, an elastic polymer that can change shape very easily. The main feature of elastomers is the high degree of elongation or elasticity and flexibility they display when supporting loads before they crack or break.
The project comes within the framework of the Basque Government’s ELKARTEK Funding Program for Collaborative Research in Strategic Areas. Three types of projects receive funding, and this one is a type-2 project that belongs to research projects having high industrial potential.
As José Santos, Head of the Injection Area at CIKATEK, pointed out, “this project is a huge opportunity for CIKAUTXO: the capabilities of conventional elastomeric components are highly optimized and it is difficult to achieve a competitive edge if the technology is not transcended”.
That is why the project is setting out to optimize rubber by using two disruptive technologies proposed by two independent departments at nanoGUNE: the Nanobiotechnology group led by Raúl Pérez-Jiménez and the Nanomaterials group led by Mato Knez.
So nanoGUNE’s Nanobiotechnology group is proposing a new ideal material for manufacturing composites and matrices in a whole host of applications, ranging from construction to medicine. “The use of this new material incorporated into elastomeric materials has not been explored that much and undoubtedly offers a potential field with a huge commercial impact for exploration, it can provide rubber with greater dynamic strength and resistance to corrosion, and to date there are no commercial products or ones tested using this blend, so the project is emerging as a great opportunity both in terms of knowledge acquisition and commercial impact going forward,” said Raúl Pérez-Jiménez. “This project also raises the possibility of a piece of multidisciplinary research when combining concepts from biotechnology, materials science, and engineering with a clear commercial and marketing approach,” he added.
Then, “an equally promising approach to improve the properties of elastomeric materials is being proposed by nanoGUNE’s Nanomaterials group; it involves manufacturing hybrid polymeric-inorganic materials in which synergies can be established, thus giving rise to new properties that these components do not display individually, or else improvements in their initial properties,” said Mato Knez. “While traditional approaches mostly involve the use of electroplating or molecular assembly of surfaces, modern approaches use techniques capable of modifying the interfacial properties of a substrate by generating hybrid materials. Hybridization can generate synergistic effects in the inorganic and polymeric phases, so it could turn into a significant mechanism for improving mechanical properties and reducing elastomer fatigue to a minimum,” he added.
Everyone agrees that “the use of these state-of-the-art technologies that have yet to be explored would without doubt allow a qualitative leap to be made towards increasing the capabilities of the components, and if this were to be achieved, competitiveness could be increased as it would be possible to continue to adhere to specifications using components that are smaller or lighter or more competitive in terms of price”.