Related news by tag Micro fabrication
NovaSpider, an innovative technology recently protected through a patent application
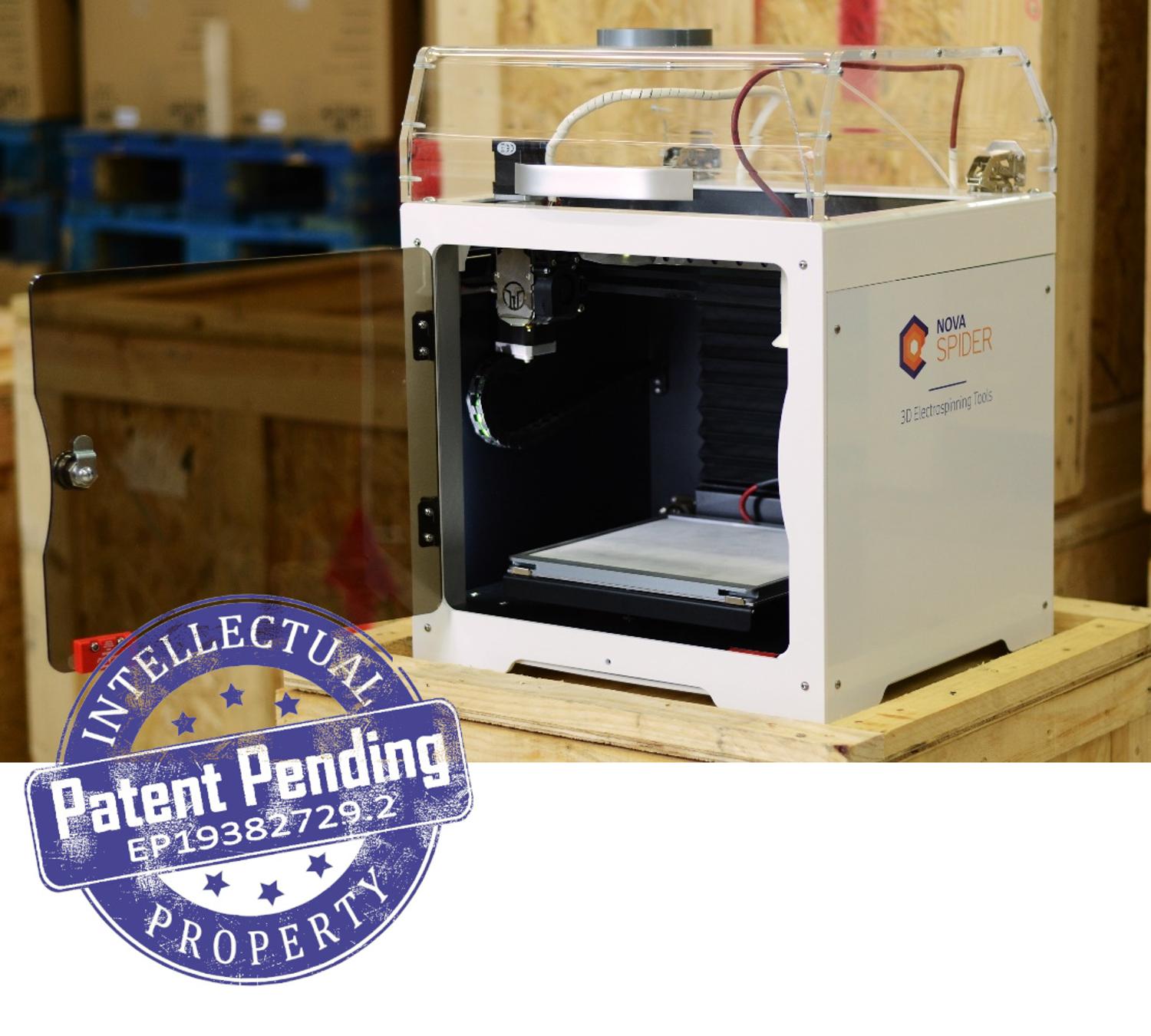
The application fields of the structures generated by NovaSpider are versatile and promising. Using polymer nanofibres, whose nature, diameter, appearance and morphology can be modulated in a simple and efficient way, the device allows designing composite materials that are robust, light, porous and offer a high specific surface area. Structures of this type arouse huge interest in regenerative medicine, where they are used as scaffolding in tissue regeneration; in the biomedical sector, where they are functionalized and used in controlled drug release and wound protection; and in the energy sector, where their role as a catalytic converter in superbatteries is being explored.
In turn, it is worth highlighting their application in the textile sector and in packaging, where the idea is to improve the conservation of foodstuffs and to replace plastics by biodegradable materials. To date, the tested sample bank is broad: sugars, proteins, collagen, gelatine, cellulose, etc., thus pointing to the great versatility of the technology. These materials, deposited onto the packaging cardboard, offer a nontoxic and specific barrier between cardboard and foodstuff. The aim is fulfilling the function provided by plastic films until now and substituting them as fully biodegradable coating.
The project is the fruit of the work conducted over the last years by Dr Wiwat Nuansing, an expert in electrospinning, and the engineer Javier Latasa, an expert in mechatronics, among other researchers and technicians in the Self-Assembly Group, led by Dr Alexander Bittner, an Ikerbasque Research Professor at nanoGUNE. The support of experts in the 3D printing industry has enabled the team to meet the highest standards and to include the sector’s latest technological developments.
The NovaSpider equipment integrates FDM/FFF additive printing technology with nanofibre manufacturing techniques involving solvent electrospinning and melt electrospinning:
- FF technology (or FDM: fused deposition material) is a currently very familiar 3D manufacturing process for components with thermoplastics. This method functions by gradually depositing layer upon layer of fused material, which solidifies on cooling to produce the desired object.
- Electrospinning is a technique that consists of subjecting a solution, usually a polymer one, to an electrostatic force produced by the electric field induced when a high voltage is applied between the solution and a grounded collector. This causes a continuous thread to be ejected out of the dissolution in the form of a jet whipping against the collector, from which a nonwoven mat of disordered nanofibres is obtained.
- Melt-electrospinning is a variant of the above. Instead of using solvents, the thermoplastic material is heated until it reaches a liquid state. As in the above technique, an electrostatic force causes a continuous fibre to be extracted from the liquid material. In this case, the fibre usually has a diameter exceeding a micron and follows a straight trajectory, without whipping, from nozzle to collector, which allows its deposition to be accurately controlled, so these microfibre structures can be reproduced by following the desired patterns.